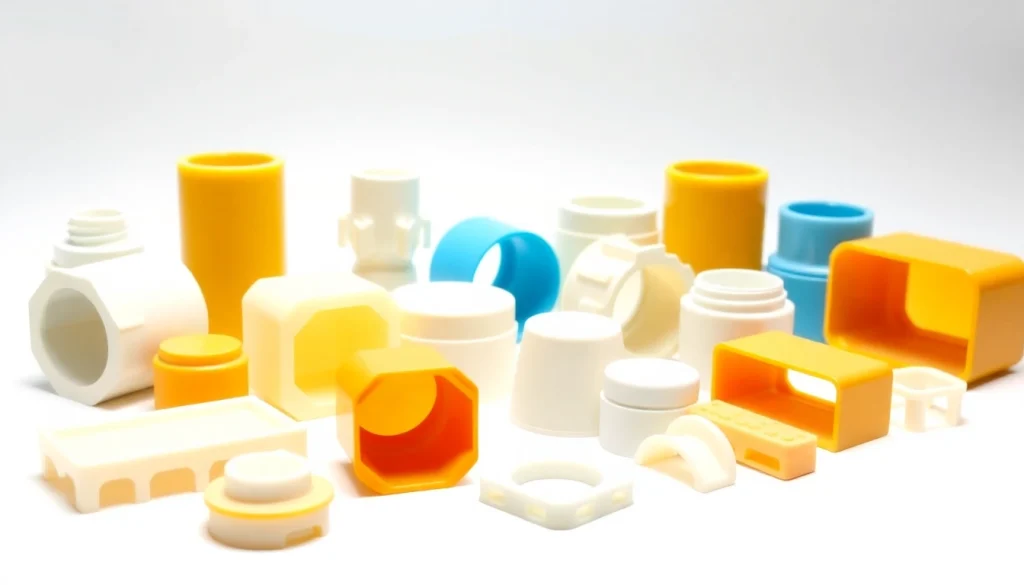
Understanding Blow Moulded Plastic Parts
What Are Blow Moulded Plastic Parts?
Blow moulded plastic parts are hollow items that are manufactured through a specialized process known as blow molding (or blow moulding). This technique involves the inflation of heated plastic into a mould to form a variety of shapes, predominantly hollow and lightweight objects. Common applications include bottles, containers, and automotive parts, making blow moulding a critical process in many industries. For those seeking to learn more, a valuable resource on blow moulded plastic parts can provide comprehensive insights.
Applications of Blow Moulded Parts in Industry
Blow molding is widely applicable across various industries. Here are some prominent applications:
- Container Manufacturing: The most recognized use of blow moulding is in creating containers for beverages, personal care products, and pharmaceuticals.
- Automotive Components: Blow moulded parts can be found in automotive fuel tanks, air intake ducts, and even specific interior parts.
- Household Items: Products such as plastic toys, furniture components, and storage containers frequently utilize blow molding.
- Packaging: While often overlooked, blow moulded packaging is fundamental in keeping products safe and secure during transport.
Benefits of Choosing Blow Moulded Plastic
The advantages of opting for blow moulded plastic parts include:
- Cost-Effectiveness: Blow moulding can be highly cost-effective for mass production, with lower per-unit costs achieved through efficient manufacturing processes.
- Design Flexibility: The blow moulding process enables manufacturers to create parts in complex shapes while maintaining structural integrity.
- Lightweight Solutions: Blow moulded plastics provide a lighter alternative to traditional materials, which can reduce transportation costs and improve user experience.
- Material Efficiency: The process minimizes waste, as excess materials are often recycled back into the production line.
The Blow Moulding Process Explained
Key Steps in Blow Moulding
The blow moulding process consists of several key steps:
- Heating the Plastic: The raw plastic material is heated until it softens enough to be manipulated, often forming a parison (a hollow tube of plastic).
- Insertion into Moulds: The softened parison is placed into a split mould that defines its final shape.
- Inflation: High-pressure air is introduced into the parison, inflating it against the inner walls of the mould to take on its final form.
- Cooling and Solidification: Once the plastic cools, it solidifies, holding the moulded shape firmly.
- Removal and Trimming: The finished product is extracted and any excess material (flash) is trimmed away.
Types of Blow Moulding: Which is Right for You?
There are three primary types of blow moulding, each suited to different applications:
- Extrusion Blow Moulding (EBM): Commonly used for producing large items such as containers and bottles, EBM involves extruding molten plastic into a mould.
- Injection Blow Moulding (IBM): This method is ideal for creating smaller, more intricate parts, utilizing injection molding techniques prior to blowing.
- Injection Stretch Blow Moulding: A combination of injection and stretch techniques, this type is often used for producing high-quality bottles with superior clarity and strength.
Common Materials Used in Blow Moulding
Diverse materials can be applied in blow moulding, including:
- Polyethylene (PE): Available in high, low, and linear forms, PE is versatile and cost-effective.
- Polypropylene (PP): Known for its resistance to heat and chemicals, PP is commonly used for automotive parts.
- Polyethylene Terephthalate (PET): Recognized for its strength and clarity, PET is often used in beverage bottles and food containers.
- Polyvinyl Chloride (PVC): PVC is utilized for a range of products due to its durability and versatility.
Selecting the Right Manufacturer for Blow Moulded Parts
Evaluating Quality and Expertise
When choosing a manufacturer for blow moulded parts, consider evaluating their quality assurance processes:
- Certifications: Look for industry-standard certifications that validate the manufacturer’s commitment to quality.
- Experience: A manufacturer with a proven track record in blow moulding is more likely to produce reliable products.
- Technology: Ensure they utilize modern equipment and techniques that enhance precision and efficiency.
Key Factors in Manufacturer Selection
Important factors to consider include:
- Production Capacity: Assessing their capability to handle your order size is essential.
- Turnaround Time: Effective communication regarding timelines can help avoid delays in the production schedule.
- Customer Support: Manufacturers that provide strong technical support and customer service can be invaluable partners.
Cost Considerations for Blow Moulded Parts
The overall cost of blow moulded parts is influenced by several factors:
- Material Costs: The choice of material can significantly impact pricing.
- Mould Design: More complex mould designs can add to production costs.
- Order Volume: Higher volumes generally lead to lower per-unit costs due to production efficiency.
Key Challenges in Blow Moulding Production
Addressing Common Production Issues
Despite its advantages, blow moulding faces specific challenges. Common issues include:
- Mould Defects: Imperfections in mould design can lead to major defects in the final product. Regular inspections and updates can mitigate this risk.
- Inconsistency in Material: Variations in material quality can cause discrepancies in product performance. Choosing reputable suppliers is crucial.
- Pressure Control: Inaccurate air pressure during inflation can create weak spots. Implementing precise pressure monitoring systems is beneficial.
Quality Assurance Measures
Implementing comprehensive quality assurance measures ensures product reliability, including:
- Regular Testing: Perform strength and durability tests on the produced parts.
- Supplier Audits: Conduct audits of material suppliers to maintain quality standards.
- Process Documentation: Maintaining detailed process logs aids in troubleshooting and improving workflows.
Technological Advances in Blow Moulding
Continuous advancements in blow moulding technology are enhancing production capabilities:
- 3D Printing for Prototyping: 3D printers facilitate rapid prototyping, allowing for design adjustments before full-scale production.
- Smart Sensors: Incorporating smart sensors in manufacturing equipment can help in real-time monitoring of production parameters.
- Recycling Innovations: New methods for recycling scrap plastics used in blow moulding can reduce waste and lower costs.
Future Trends in Blow Moulded Plastic Parts
Sustainability Practices in Blow Moulding
As the global focus shifts towards sustainability, the blow moulding industry faces new challenges and opportunities:
- Use of Recycled Plastics: Integrating recycled materials into production processes can reduce the environmental impact.
- Biodegradable Alternatives: The exploration of biodegradable materials that still meet performance standards is on the rise.
- Energy Efficiency Improvements: Investments in energy-efficient machinery and processes minimize energy consumption during manufacturing.
Innovations in Blow Moulding Technology
Innovation continues to drive the blow moulding sector:
- Advanced Moulding Techniques: Emerging technologies such as 3D blow moulding are paving the way for unprecedented design flexibility.
- Enhanced Automation: Automation is improving efficiency and reducing labor costs across production lines.
- Integration with IoT: The Internet of Things (IoT) is set to revolutionize process monitoring and data collection, leading to smarter manufacturing environments.
Market Predictions for Blow Moulded Products
Industry analysts project significant growth for blow moulded products driven by increased demand in various sectors:
- E-Commerce Packaging: The rise of online shopping fuels the need for innovative, efficient, and highly functional packaging solutions.
- Electronics Industry Utilization: There’s a growing trend toward using blow moulded parts in electronics packaging due to their protective qualities.
- Sustainable Product Lines: Companies focusing on sustainability will increasingly rely on blow moulding to produce eco-friendly options.